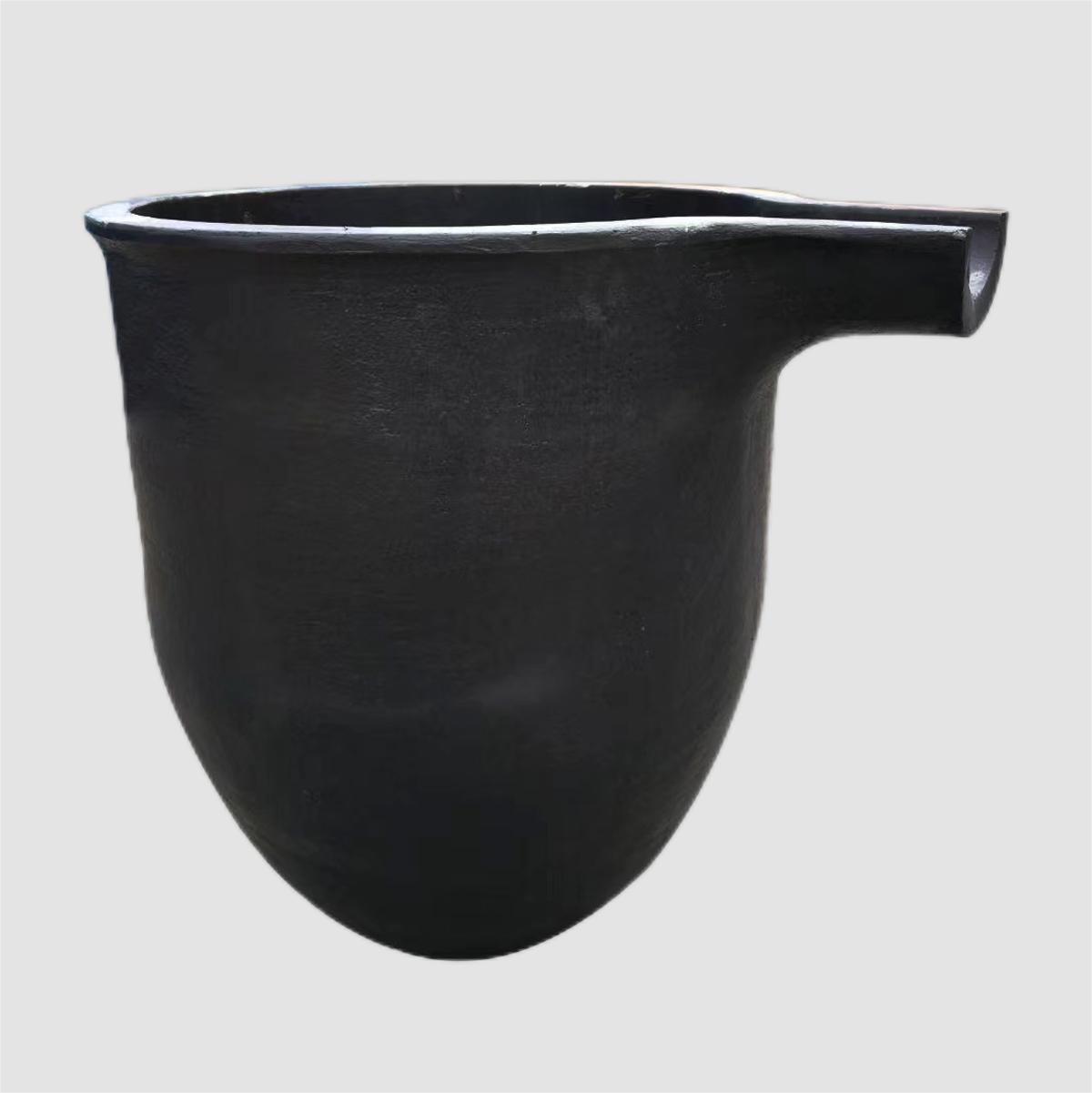
1.4 Вторичное шлифование
Паста измельчен, заземляется и размер в частицах десятков до сотен микрометров, а затем смешивается равномерно. Он используется в качестве нажатиющего материала, называемого нажимающим порошком. Оборудование для вторичного шлифования обычно использует вертикальную роликовую мельницу или шариковую мельницу.
1.5 Формирование
В отличие от обычной экструзии и формования,Изостатический нажающий графитформируется с использованием технологии холодной изостатической прессы (рис. 2). Заполните порошок сырья в резиновую форму и уплотняйте порошок с помощью высокочастотной электромагнитной вибрации. После герметизации вакуум из частиц порошка, чтобы исчерпывать воздух между ними. Поместите его в контейнер с высоким давлением, содержащий жидкую среду, такую как вода или масло, подчеркивайте его на 100-200 МПа и нажмите на цилиндрический или прямоугольный продукт.
Согласно принципу Паскаля, давление оказывается на резиновую плесень через жидкую среду, такую как вода, и давление равно всем направлениям. Таким образом, частицы порошка не ориентированы в направлении заполнения в форме, но сжимаются в нерегулярном расположении. Следовательно, хотя графит является анизотропным по кристаллографическим свойствам, в целом изостатический нажающий графит является изотропным. Сформированные продукты имеют не только цилиндрические и прямоугольные формы, но также цилиндрические и типичные формы.
Изостатическая прессовательная формовочная машина в основном используется в индустрии металлургии порошка. Из-за спроса в высококлассных отраслях, таких как аэрокосмическая, ядерная промышленность, жесткие сплавы и высоковольтные электромагнитные, разработка изостатической технологии прессования очень быстрая, и обладает способностью производить холодные изостатические нажимающие машины с рабочим цилиндром внутреннего диаметра 3000 мм, высотой 5000 мм и максимальным рабочим давлением 600 мм. В настоящее время максимальные спецификации холодных изостатических прессовающих машин, используемых в углеродной промышленности для производства изостатического нажатого графита, составляют φ 2150 мм × 4700 мм, с максимальным рабочим давлением 180 МПа.
1.6 Выпекание
Во время процесса обжарки возникает сложная химическая реакция между заполнителем и связующим, заставляя связующего разложения и высвобождения большого количества летучих веществ, а также подвергается реакции конденсации. На низкотемпературной стадии предварительного нагревания сырой продукт расширяется из-за нагрева, а в последующем процессе нагрева объем сокращается из-за реакции конденсации.
Чем больше объем необработанного продукта, тем сложнее высвобождать летучие вещества, а поверхность и внутренняя часть сырого продукта подвержены температурным различиям, неравномерному тепловому расширению и сокращению, что может привести к трещинам в сыром продукте.
Из -за своей тонкой структуры изостатический нажающий графит требует особенно медленного процесса обжарки, а температура внутри печи должна быть очень равномерной, особенно на стадии температуры, где летучие вещества асфальта быстро разряжаются. Процесс нагрева должен выполняться с осторожностью, при этом скорость нагрева не превышает 1 ℃/ч, а разность температуры в печи менее 20 ℃. Этот процесс занимает около 1-2 месяцев.
1,7 Пепирация
Во время обжаривания летучая вещество углярной смолы выгружается. Прекрасные поры остаются в продукте во время сброса газа и сокращения объема, почти все из которых представляют собой открытые поры.
Чтобы улучшить объемную плотность, механическую прочность, проводимость, теплопроводную мощность и химическую стойкость продукта, можно использовать метод пропитания давления, который включает в себя пропитывание угольной смолы в внутреннюю часть продукта через открытые поры.
Продукт должен быть предварительно разогрет сначала, а затем пылесос и дегрессирован в резервуаре для пропитки. Затем в резервуар для пропитки добавляется расплавленный асфальт угля и подчеркивается, чтобы позволить асфальту пропитывающего агента войти в внутреннюю часть продукта. Обычно изостатический нажающий графит подвергается множеству циклов жарки пропитки.
1.8 Графитизация
Нагрейте кальцинированный продукт примерно до 3000 ℃, упорядочивайте решетку атомов углерода и заполните преобразование от углерода в графит, который называется графитизацией.
Методы графитизации включают метод Acheson, метод соединения внутреннего теплового ряда, высокочастотный метод индукции и т. Д. Обычный процесс Acheson занимает приблизительно 1-1,5 месяца для загрузки продуктов и выброса из печи. Каждая печь может обрабатывать несколько тонн до десятков тонн жареных продуктов.
Время публикации: сентябрь-29-2023